What is PUWER?
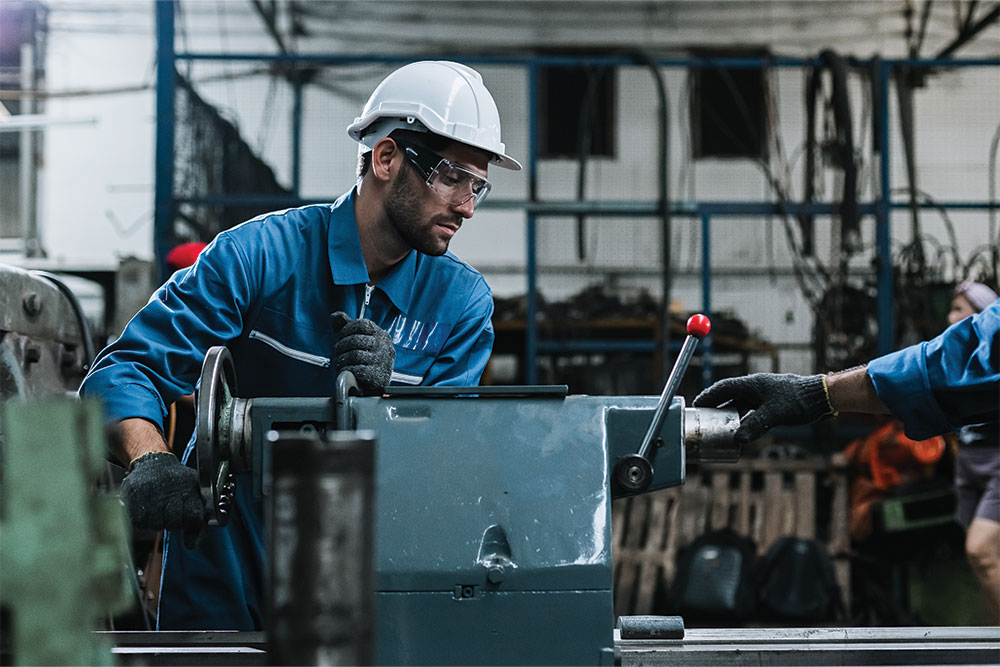
The safety of equipment and machinery in workplaces across the UK is regulated by the Provision and Use of Work Equipment Regulations (PUWER) 1998. These regulations are vital to ensuring that workplaces remain safe, productive, and compliant with health and safety laws. Their importance becomes starkly clear when considering the statistics: in 2022/23, 138 people were fatally injured at work, with 8% of these fatalities resulting from contact with moving machinery. Additionally, 561,000 workers sustained non-fatal injuries. These figures underscore the critical role PUWER plays in safeguarding lives and reducing workplace risks.
This comprehensive guide explores what PUWER entails, the responsibilities it places on employers, and how organisations can ensure compliance with these essential regulations.
What Does PUWER Stand For?
PUWER is an acronym for the Provision and Use of Work Equipment Regulations. First introduced in 1992 and updated in 1998, these regulations are a cornerstone of UK health and safety legislation. They outline the responsibilities of employers, business owners, and anyone in control of workplace equipment to ensure it is safe for use.
Whether in manufacturing plants, schools, healthcare facilities, or construction sites, PUWER applies to all workplaces and aims to minimise risks associated with machinery and tools.
What Are the PUWER Regulations?
PUWER regulations exist to safeguard anyone who interacts with machinery and equipment in the workplace. This includes employees, contractors, self-employed individuals, and even members of the public who might be affected indirectly.
Key points of the PUWER regulations include:
-
Suitability: Equipment must be appropriate for its intended use and operating conditions.
-
Maintenance: All equipment must be regularly maintained to ensure it remains safe for use.
-
Inspections: Equipment requires routine inspections by competent individuals to verify safety and functionality.
-
Training: Only trained and competent individuals should operate machinery or equipment.
What Does PUWER Cover?
PUWER applies to a broad spectrum of equipment, including:
-
Machinery and power tools
-
Appliances and office equipment
-
Installations like conveyor belts
-
Vehicles such as forklifts and dumper trucks
Industries and environments where PUWER applies include:
-
Manufacturing and industrial sites
-
Construction and building sites
-
Retail and hospitality venues
-
Educational institutions
-
Healthcare facilities
-
Offshore oil and gas installations
Importantly, PUWER also applies to equipment used for work purposes at home. However, it does not govern equipment used by the public, such as compressed air machines at petrol stations. These are instead regulated by the Health and Safety at Work Act 1974.
What Is a PUWER Inspection?
A PUWER inspection is a detailed examination of workplace equipment to ensure it is safe to use and compliant with the regulations. The scope of an inspection depends on the type of equipment and its usage frequency. Simple tools may require a quick visual check, while complex machinery might need thorough inspections, sometimes involving dismantling.
Inspections typically cover:
-
Equipment condition and maintenance
-
Safety measures such as guards and emergency stops
-
Warning devices and alarms
-
Proper use of personal protective equipment (PPE)
-
Electrical safety of installations
A detailed record of inspections must be maintained. Depending on the type of equipment, inspections may need to occur daily, weekly, or at other regular intervals.
How to Comply with PUWER
Compliance with PUWER involves several critical steps:
-
Ensure Suitability: Equipment must be appropriate for its specific tasks and operating conditions.
-
Routine Inspections: Establish a schedule for regular inspections carried out by qualified individuals.
-
Maintenance: Perform ongoing servicing and repairs to ensure equipment remains in safe working order.
-
Training: Provide adequate training to all employees who operate machinery or tools.
Additional measures to ensure compliance include:
-
Installing emergency stop systems and warning devices
-
Using appropriate PPE
-
Marking hazards with visible safety labels
-
Isolating electrical sources that could pose risks
Special requirements exist for mobile work equipment and power presses. For instance, forklifts must undergo checks to ensure they are safe for carrying people, while power presses require detailed and regular examinations.
PUWER and Other Regulations: What Is the Difference Between PUWER and LOLER?
While PUWER focuses on the general safety of workplace equipment, the Lifting Operations and Lifting Equipment Regulations (LOLER) 1998 specifically address the safety of lifting equipment, such as cranes and hoists. Both sets of regulations often overlap, particularly in industries like construction and manufacturing where lifting equipment is common.
How Is PUWER Enforced?
Health and safety inspectors play a key role in enforcing PUWER. They can issue two types of notices:
-
Improvement Notices: Issued when equipment is poorly maintained, inadequately inspected, or presents safety risks. Organisations are given at least 21 days to address the issues.
-
Prohibition Notices: Issued when equipment poses an immediate danger. The equipment must not be used until the problems are resolved.
Failure to comply with these notices can lead to severe consequences, including financial penalties and legal action.
Why PUWER Compliance Matters
Poorly maintained or misused equipment can have devastating consequences, ranging from serious injuries to fatalities. Compliance with PUWER not only protects workers but also shields businesses from financial losses due to equipment downtime, fines, or legal repercussions.
To support compliance efforts, organisations should ensure their employees are trained to understand the risks and safe operation of equipment. For instance, investing in electrical safety training courses can significantly reduce risks in the workplace.
Keep Your Workplace Safe
Understanding and adhering to PUWER regulations is essential for creating a safe and compliant workplace. Whether you're managing a factory floor, an office, or a healthcare facility, implementing the principles of PUWER can save lives, prevent injuries, and protect your business operations.
By ensuring your equipment is safe and your staff are trained, you contribute not just to a safer workplace but to a culture of responsibility and care. Stay proactive with regular inspections, proper maintenance, and comprehensive training to meet PUWER standards effectively.
If you’re looking for more information or training resources, consider exploring our range of courses designed to enhance workplace safety and compliance.
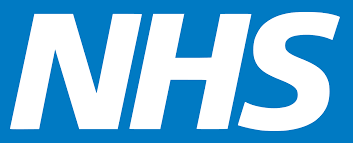
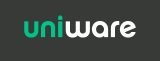
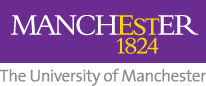
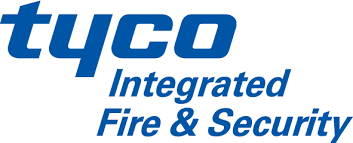
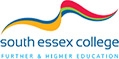

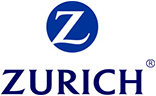
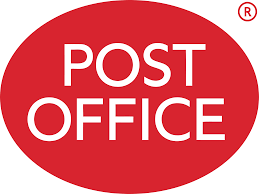






Validate your login